AIM – our method for continuous improvements
For us, AIM stands for objectives, purpose and ambition. It is also the name of our working method – the Always Improve Method.
This method consists of four principles that together create the right conditions for continuous improvement. They are a standardized approach, short lead times, quality and environment, and participation – four equally important elements that give us clear structures to work by at different levels throughout the entire process.
Our aim is to be Sweden’s foremost OEM supplier and contract manufacturer. The AIM method helps us to maintain focus on continuous development and improvement of our work processes from the resource, costs and environmental perspectives in order to generate competitive edge for our customers and create leaner and greener production.
Participation
Our employees are, of course, our most important resource. Their participation in and commitment to continuous improvement is crucial. Breaking down our objectives ensures we are all on the same page about where the company is heading, and lean production creates an open and results-oriented company climate. Results are recorded on the daily control boards so they can be followed up, and all personnel are encouraged to contribute to the improvements log. Cross-function teams meet regularly to discuss improvements and solve any problems.
Quality and Environment
We work with prevention and assuring compliance with quality and environmental standards through the ISO systems and certifications. Any problems we identify, we solve with the aid of the methods “4M”, “the 5 Whys” and “Fishbone analysis”. Through our improvements systems, our employees can themselves provide suggestions for improvements. Each step in the process is validated and verified to quality-assure the work flow. Productive maintenance also makes quality and reliability work the concern of all our employees.
Short lead times
All our manufacturing is customer-driven, and through value stream analyses, we create work processes with simple, pulled flows, which means that we avoid unnecessary inventory and don’t waste precious time. Our logistics organization works continuously to assure and optimize the quality of our subcontractors. This is essential for being able to keep to the short lead times we have.
Standardized work
Our operations feature efficient work places with well-established routines, discipline, order and attention to detail. We create this through the use of a standardized approach, “SOP”, “5S” and “visualised, lean leadership”. Operation cards, sequence lists and daily control boards provide clear instructions and a rapid flow of information. Everything is measured and recorded so that it can be evaluated, followed up and improved.
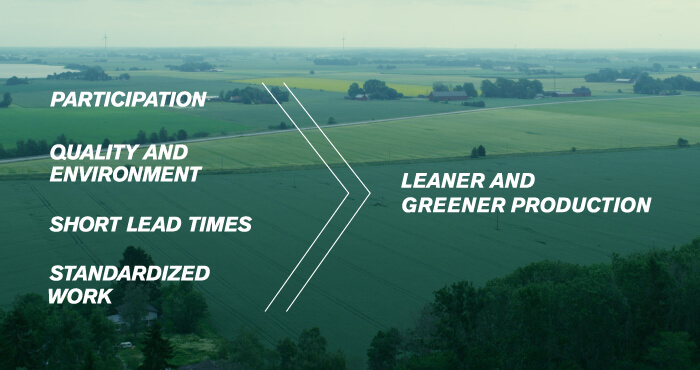